Spotlight on Logistics: Top 4 Areas Suffering from Manual IT Processes
The logistics industry is critical for the smooth functioning of the global economy. At its core, logistics ensures that products get from one place to another, on time and in the right condition. Despite the significance of this sector, many logistics processes remain manual and time-consuming. However, with the advent of Robotic Process Automation (RPA) and other automations, there’s significant potential to streamline and improve these tasks.
Understanding the Pain Points
To shed light on the areas within logistics facing the most manual IT processes, we conducted a comprehensive survey among 300 logistics experts. The results are illuminating, revealing the key challenges that industry professionals currently grapple with:
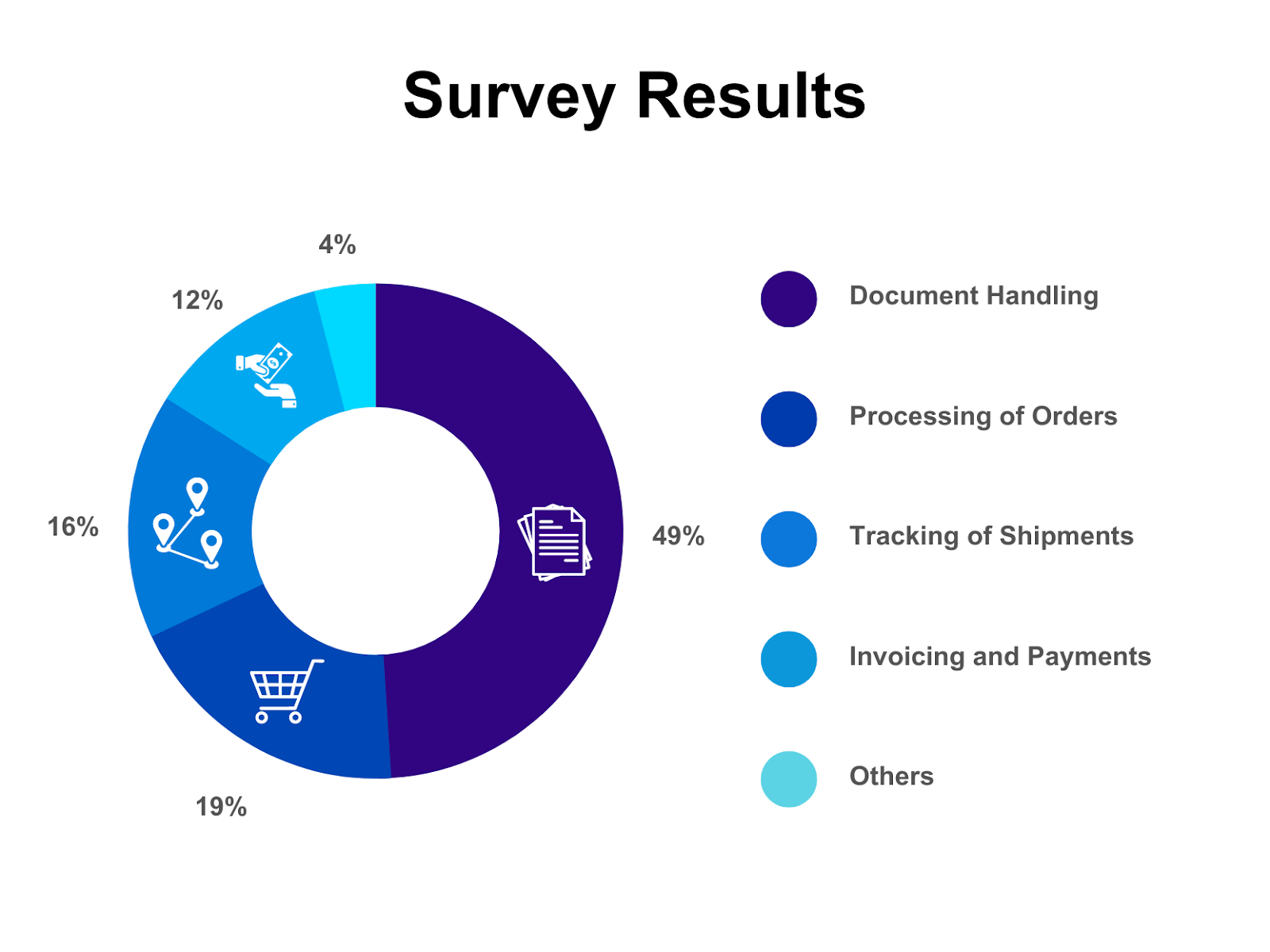
These insights underscore the pressing need for innovation in the logistics sector. Now, let’s delve into the top four areas in logistics that are ripe for automation and explore the benefits they can bring.
1. Processing of Orders (incl Document Extraction)
Many companies still depend on human intervention to input, verify, and manage order information. This often involves manually extracting information from PDFs, emails, or other documents, leading to inefficiencies and errors.
2. Document Handling/Processing
Managing the myriad of documents in logistics – from customs declarations to invoices – requires meticulous organization and tracking. Without automation, this becomes a complex task that requires constant attention and can easily lead to misplaced or overlooked documents.
3. Tracking of Shipments
Manually tracking shipments and updating schedules is labor-intensive and may not provide real-time information, especially when multiple shipments and routes are involved.
4. Invoicing and Payments
Traditionally, invoicing and payment processes have required manual data entry, verification, and reconciliation. Such manual methods can lead to delays, miscommunications, and even financial discrepancies.
Benefits of Using RPA/Automations in Logistics
Faster Processing of Data:
Automation significantly speeds up data processing. For example, RPA can instantly extract and input order information from a PDF into a system, whereas manually doing so could take much longer.
Less Resources Required:
With RPA handling repetitive tasks, there’s a reduced need for human resources to manage these processes. This leads to cost savings and allows personnel to focus on more strategic, value-added tasks.
Better Information Quality:
Automated processes reduce the likelihood of human error. This means that the data in the system is more accurate and up-to-date, leading to better decision-making.
Higher Customer Satisfaction:
Automation ensures that processes run smoothly, on time, and with fewer errors. When orders are processed efficiently, shipments are tracked accurately, and invoices are handled promptly, customers are more likely to be satisfied with the service they receive.
The Transformative Potential of Process Automation in the Future of Logistics
In conclusion, automation, especially through RPA, offers a promising avenue for logistics companies to optimize their operations. By addressing these five areas with automation, businesses can reap significant rewards in terms of efficiency, accuracy, and customer satisfaction. The future of logistics will undoubtedly be shaped by how well the industry integrates and leverages these technological advances.